Basic Info.
Process
Forming Process
Industry
Metal Stamping Parts
Tolerances
0.1mm
Customized
Customized
Surface Treatment
Painting/Powder Coating/Sand Blast/Anodise
Tolerance
ISO2768-F
Transport Package
Plywood
Origin
Qingdao
HS Code
7326909000
Production Capacity
500ton
Product Description
Sheet Metal Fabrication Aluminum Stainless Steel Carbon Steel Laser Cutting Machining Punching Bending Welding Stamping Parts
Product Display
Welding Advantages:
1. argon tungsten arc welding:
1) Argon can effectively isolate air, is insoluble in metal and does not react with metal. During welding, the arc can also automatically remove the oxide film on the surface of the molten pool. Therefore, it can successfully weld non-ferrous metals, stainless steel and various alloys that are easy to oxidize, nitride and chemically active.
2) Tungsten electrode arc is stable, and dozens of it can still burn stably under a small welding current (less than 10a), which is especially suitable for the welding of thin plates and ultra-thin materials.
3) The heat source and filler wire can be controlled separately, so the heat input is easy to adjust, and welding at various positions can be carried out. It is also an ideal method to realize single-sided welding and double-sided forming.
4) Since the droplet of filler wire does not pass through the arc, no spatter will occur, and the weld formation is beautiful.
2. MIG welding:
1) Inert gases have little chemical interaction with any metal.
2) There is no coating layer on the surface of the welding wire, and the welding current can be increased. Therefore, the penetration of the base metal is large, the welding wire melting speed is fast, and the deposition rate is high. Compared with TIG (tungsten insert gas arc welding) welding, its production efficiency is high.
3) Droplet transfer mainly adopts jet transfer. Short circuit transition is only used in thin plate welding, while drop transition is rarely used in production. When welding aluminum, magnesium and their alloys, sub jet transition is usually used. Because the cathode atomization area is large, the molten pool protection effect is good, and the weld formation is good with few defects.
4) If short-circuit transition or pulse welding method is adopted, all position welding can be carried out, but its welding efficiency is lower than that of flat welding and horizontal welding.
5) Generally, DC reverse connection is adopted, so that the arc is stable, the droplet transfer is uniform, the splash is less, and the weld formation is good.
3. CO2 welding:
1) CO2 arc has strong penetration, which can increase the blunt edge of the groove and reduce the groove during thick plate welding; High welding current density and high welding wire melting rate; Generally, slag cleaning is not required after welding, so the productivity of CO2 welding is about 1 ~ 3 times higher than that of electrode arc welding.
2) Pure CO2 welding can not achieve jet transfer within the general process range. It is commonly used: short-circuit transfer and drop transfer. Jet transfer can be obtained only after mixed gas is added.
3) Short circuit transfer can be used for all position welding, and the welding quality of thin-walled components is high and the welding deformation is small.
4) It has strong rust resistance, low hydrogen content in weld, and little tendency to cold crack when welding low alloy high strength steel.
5) CO2 gas is cheap, and the cleaning of weldments before welding can be simplified. Its welding cost is only 40% ~ 50% of that of submerged arc welding and electrode arc welding.
4. submerged arc welding:
1) High welding productivity
2) Good weld quality
3) Low welding cost
4) Good working conditions
5) Wide welding range
5. resistance welding:
1) the two metals are heated internally under pressure to complete the welding. Whether it is the formation process of the welding joint or the formation process of the joint surface, its metallurgical problems are very simple.
2) Due to heat concentration and short heating time, the heat affected zone is small, and the deformation and stress are small. Generally, it is not necessary to consider the correction or heat treatment process after welding.
3) Simple operation, easy to realize mechanized and automated production, no noise and smoke, good working conditions.
4)With high productivity, it can be incorporated into the assembly line together with other manufacturing processes in mass production.
6. manual electrode arc welding:
1) The equipment used is relatively simple, relatively cheap and portable.
2) Gas protection is not required.
3) Flexible operation and strong adaptability.
4) It has a wide range of applications and is suitable for the welding of most industrial metals and alloys.
Production Process
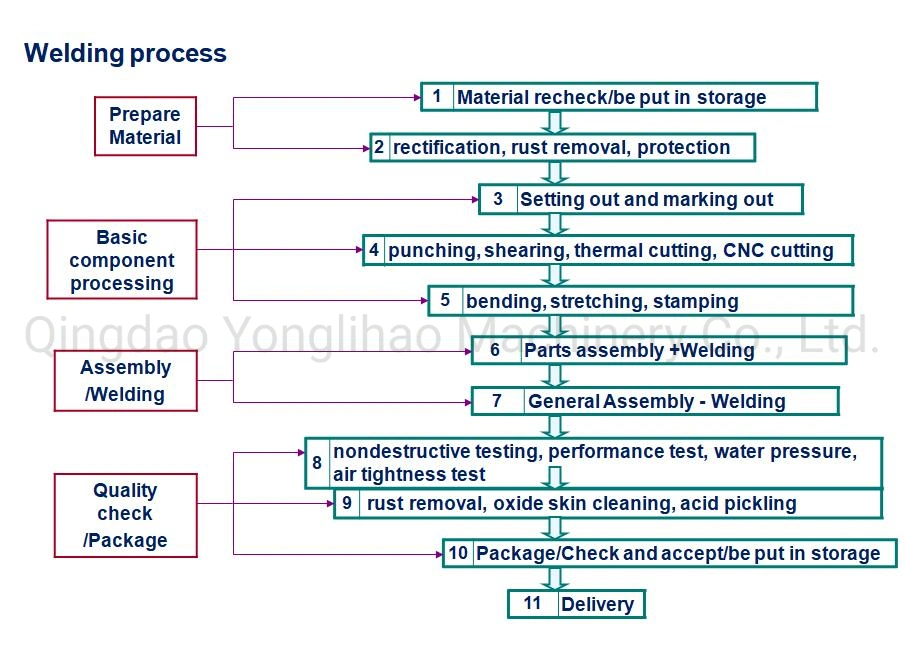
Quality Control
In Yonglihao, every staff emphasizes quality is first. Testing report and samples of all products will be kept by our quality control department.
>> Receiving inspection to raw material
All materials must be provided with suppliers' certificates, and have to pass the receiving inspection before starting production. Occasionally, material samples will be sent to independent lab for specific test to meet customers' demands. All materials have to be tagged and classified, so the original source could be traced at any time during production processes.
>> Producing inspection
Every phase of production processes will be monitored by producing inspection. The first product shall accept test in every phase of production process. Only it completes the test and confirmed by quality control manager, mass production could be operated. Every producing operator will implement constant tests during production processes, including size-measuring, observing the appearance.
>>Final inspection
Products of Yonglihao only can get out of the warehouses after all files signed and sealed.
Warehouse and Shipment
RFQ:
Q1:Where can I get product & price information?
A1:Send us inquiry e-mail or add us whatsapp, we will contact you as we receive your mail.
Q2:How long can i get the sample?
A2:Depends on your specific items, within 3-7 days is required generally.
Q3:What kinds of information you need for quote?
A3:Kindly please provide the product drawing in PDF, and will be better you can provide 3D drawing in STEP or IGS format.
Q4: What shall we do if we do not have drawings?
A4:Please send your sample to our factory, then we can copy or provide you better solutions. Please send us pictures or drafts with dimensions (Length, Hight, Width), CAD or 3D file will be made for you if placed order.
Q5: How can we know the chemical component of your products is according to our request?
A5: When we offer samples or batch parts, we will also send you our material list from our material factory, it shows more detailed.
Q6: How to guarantee your final size can meet our drawing request?
A6: we will make moulds according to your 3D drawing. And we also do sampling when batch production start, to make sure the final dimension can meet your request.
Q7: How to make sure the color after painting or powder coating can be correct?
A7: We have color card with different color number, such as RAL9016, we will contrast the sample surface and color card, to make sure the final surface effect is correct.
Q8: Generally, how do you packing the goods?
A8: normally, for inner package: the goods is nude, for outer package: carton + plywood.
Q9: If we find the defect products exist in the batch parts, how to do?
A9: Yes,your caution is very good, in fact, when batch production, we need do sampling. Before shipment, we also do testing to make sure the quality is ok. If you found several defect product exists, pls take photos and send your quality feedback, we will check and send you qualified products. But pls be assured that our products is qualified, unless caused by the worker's mistake to place.
Product Material | Q235/ Q345/ C10/ C20/ C45/ 16Mn etc. AL6061/ AL6063/ AL5754/ AL5052 etc. SUS201/ SUS303/ SUS304/ SUS316/ SUS316L etc. H57/ H58/ H59/ H62 etc. |
Accuracy | 0.1mm |
Capacity | Parts :1million /month |
Design software | 3D:PROE/ UG/ SOLIDWORKS 2D: AutoCAD/ PDF/JPEG |
Surface Treatment | Powder coating/ Hot galvanized/ Painting/ Polishing/ Brushing/ Chrome plating/ Nickel plated etc. |
Test Equipment | Hardness tester/ Chemical analysis/ Digital Measuring Projector etc. |
Thickness | 0.1-20mm or other special available |
Lead time | 15-50 days according to products |
Standard | ANSI/ API/ BS/ DIN/ JIS/ GB etc. |
Equipment |
|
Productions Cover | Light product/ Construction industry product/ Valve product/ Auto spare product/ Motor car products/ Equipment spare product/ Furniture products etc. |
Product Display
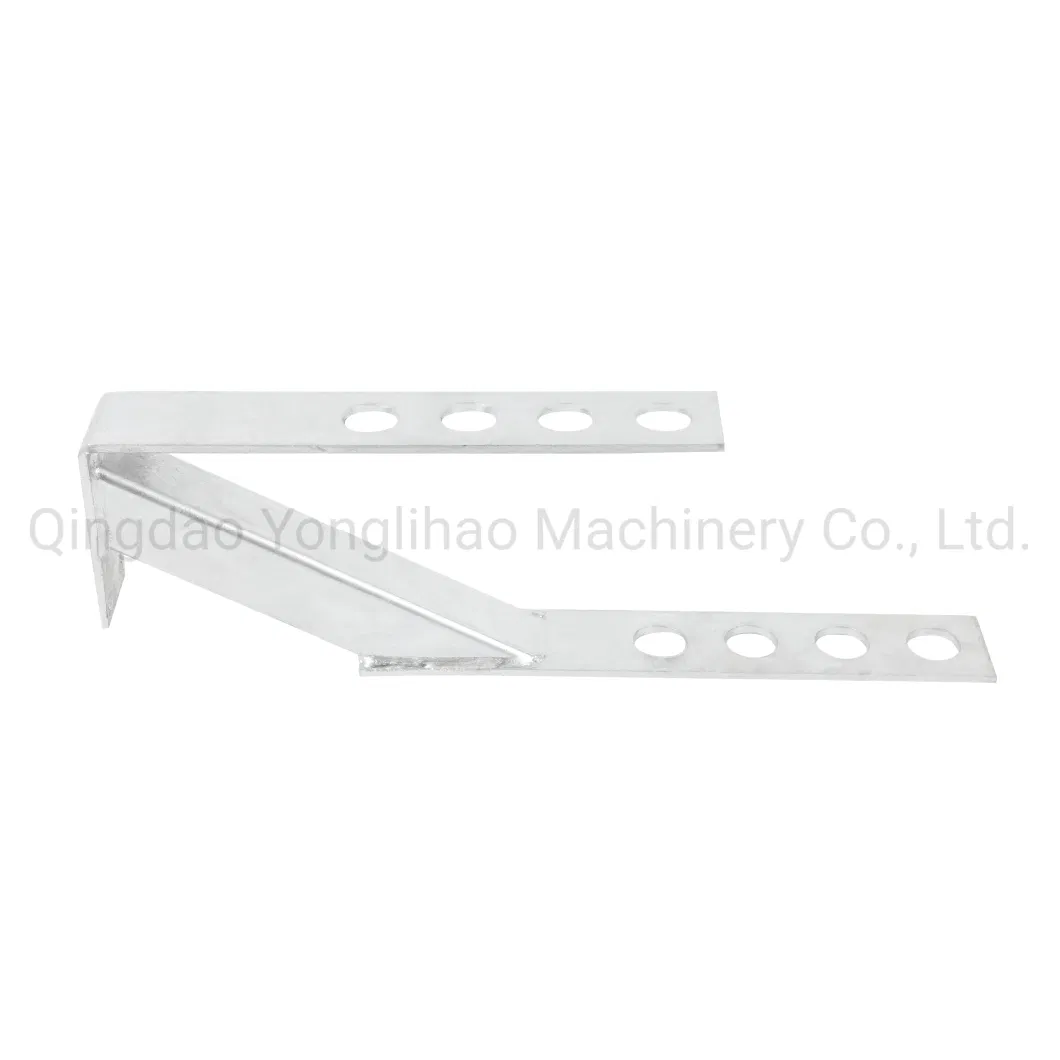
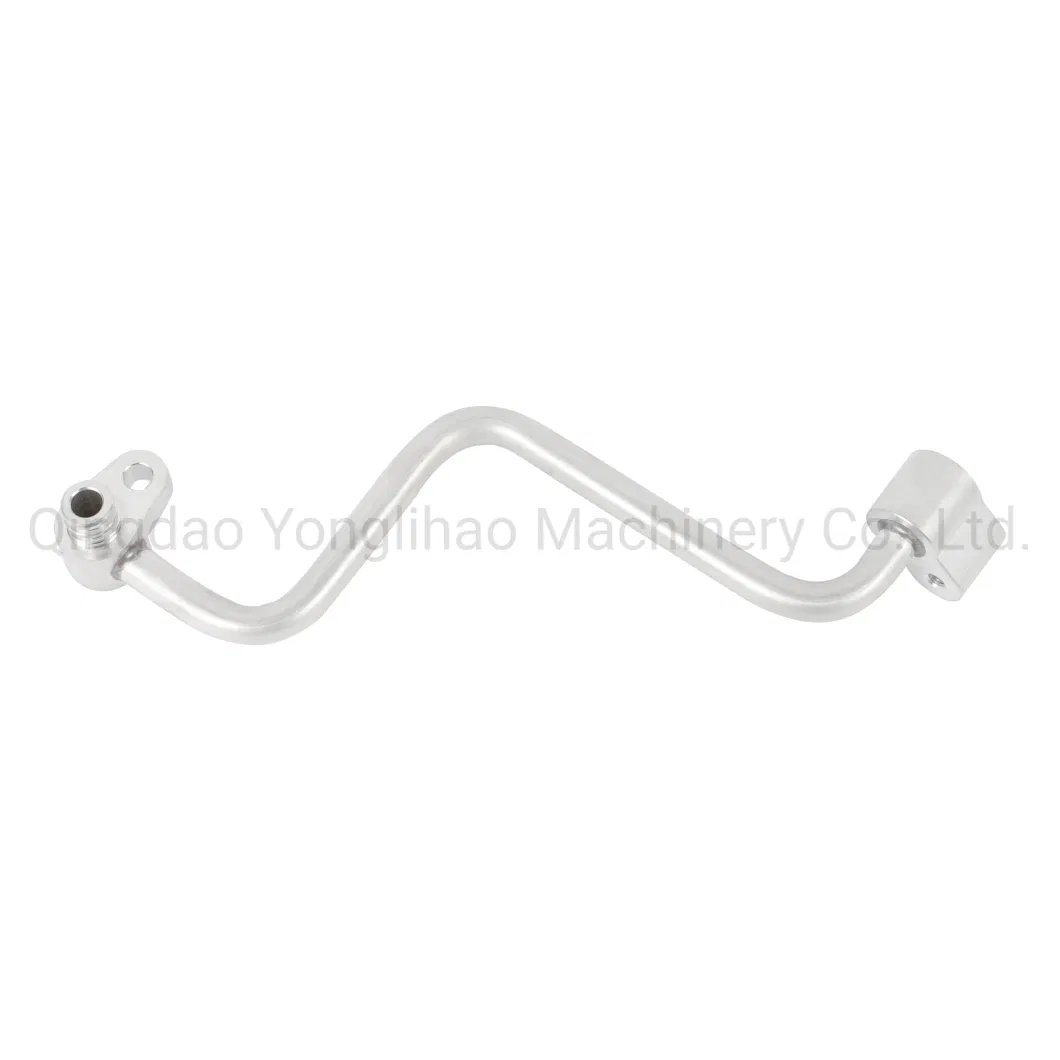
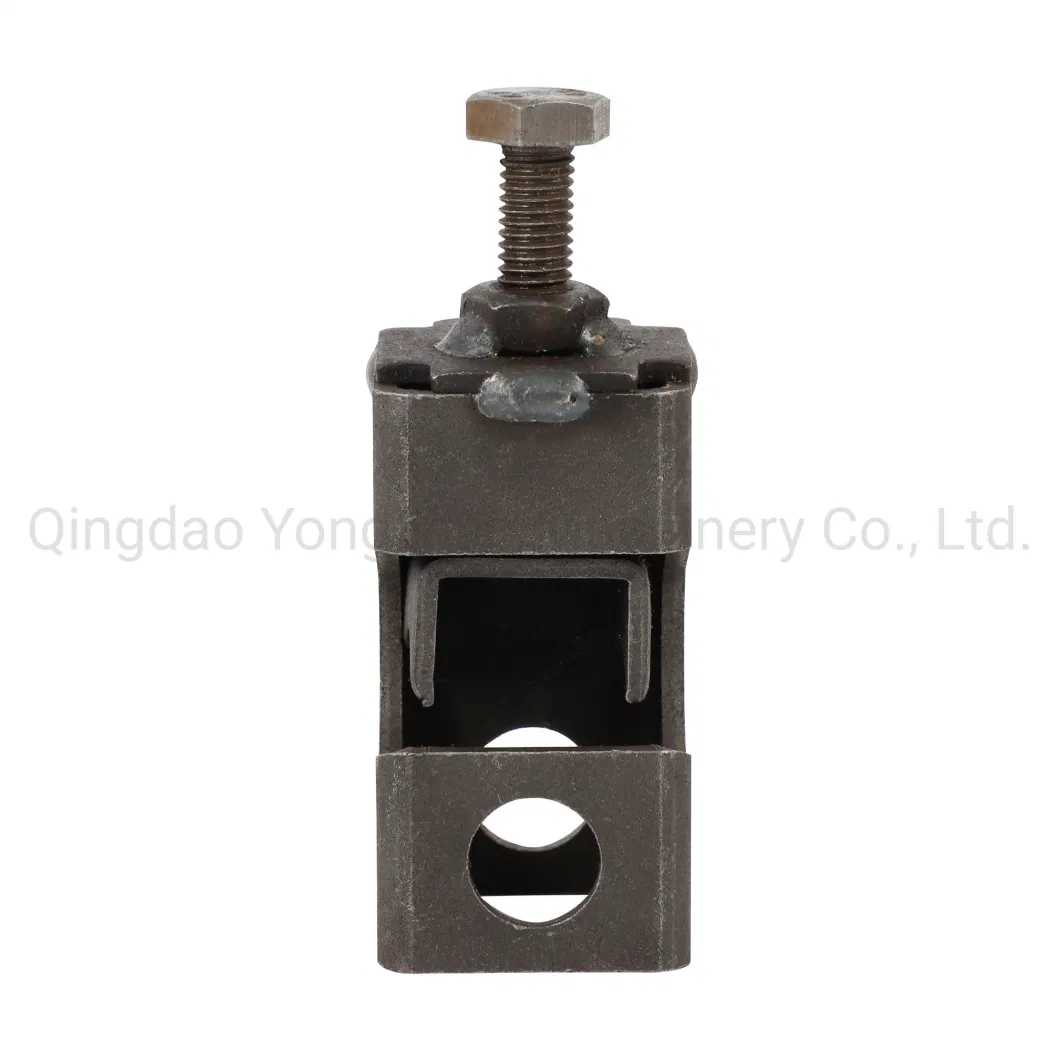
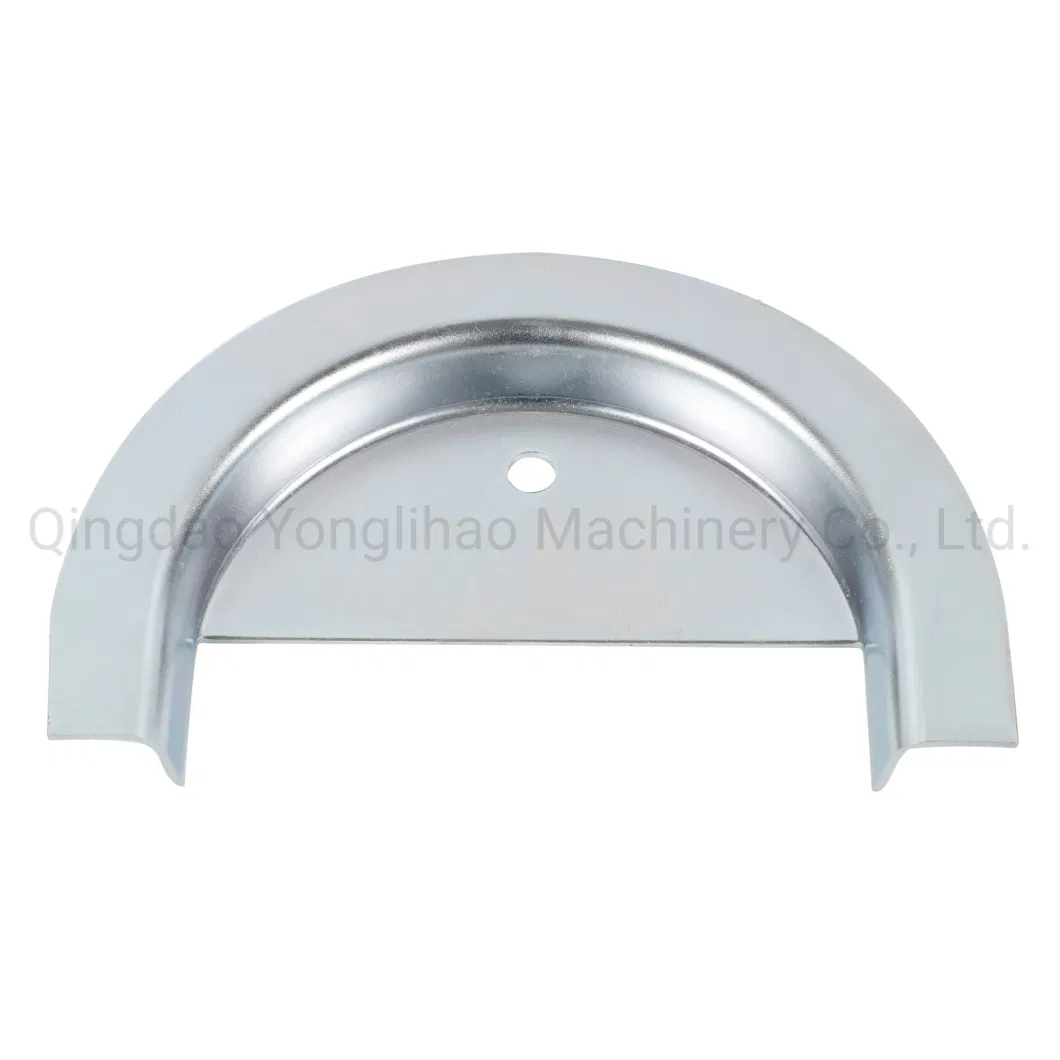
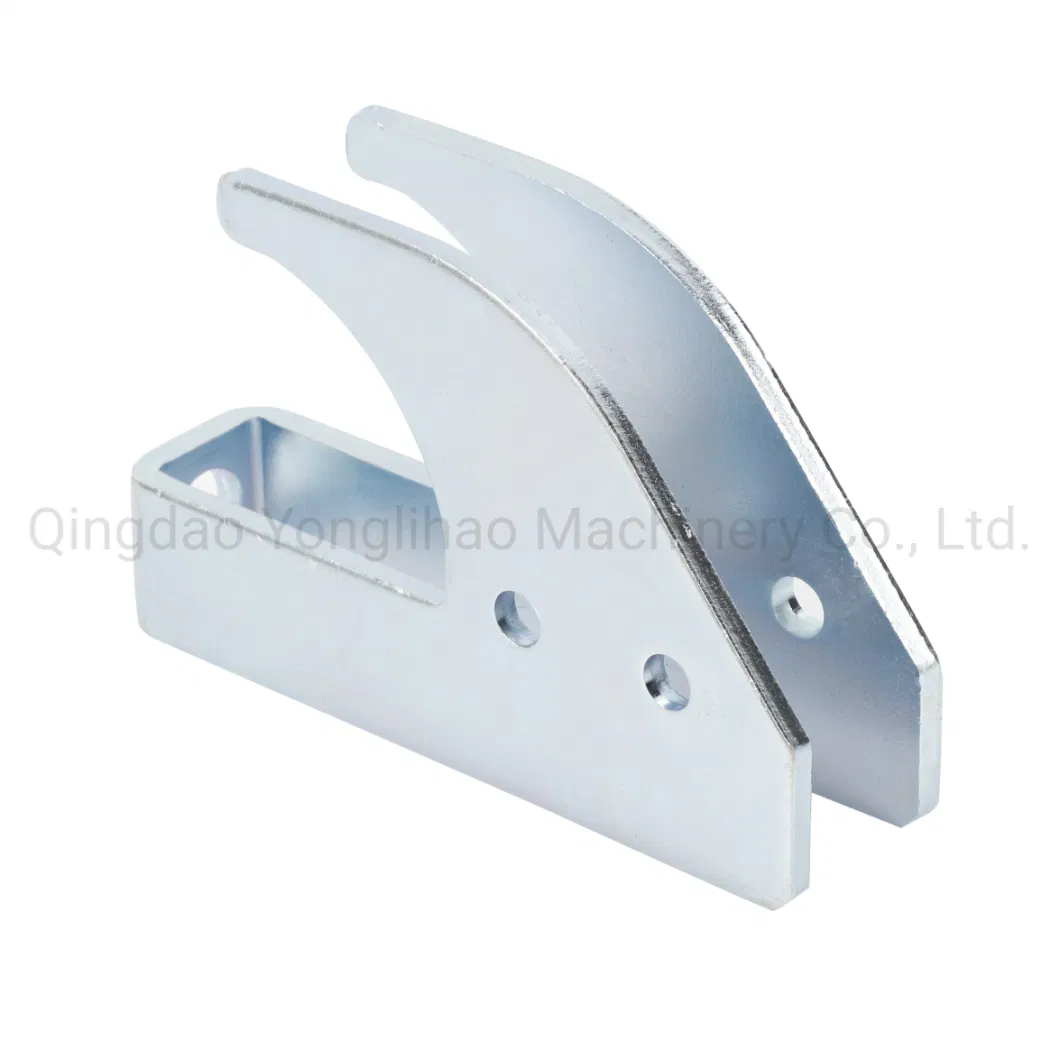
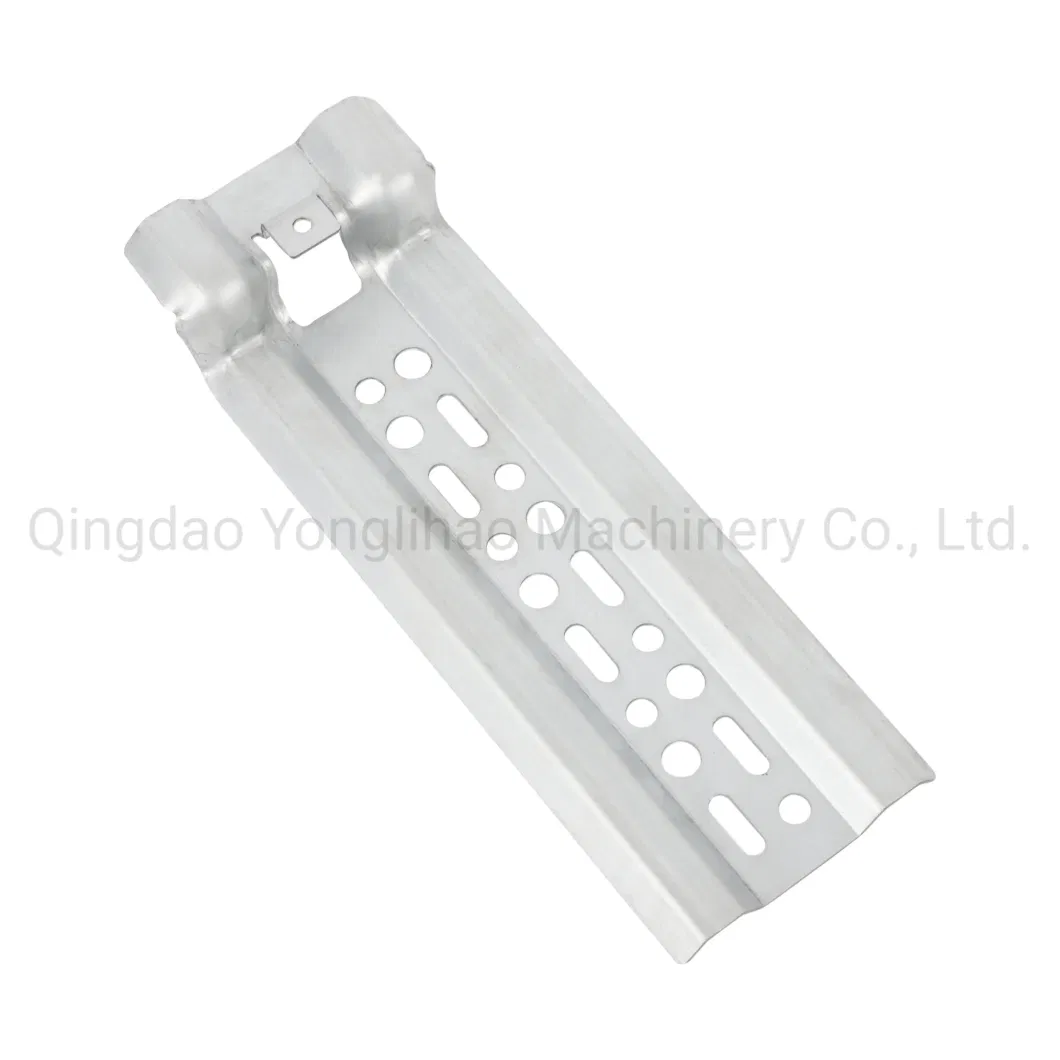
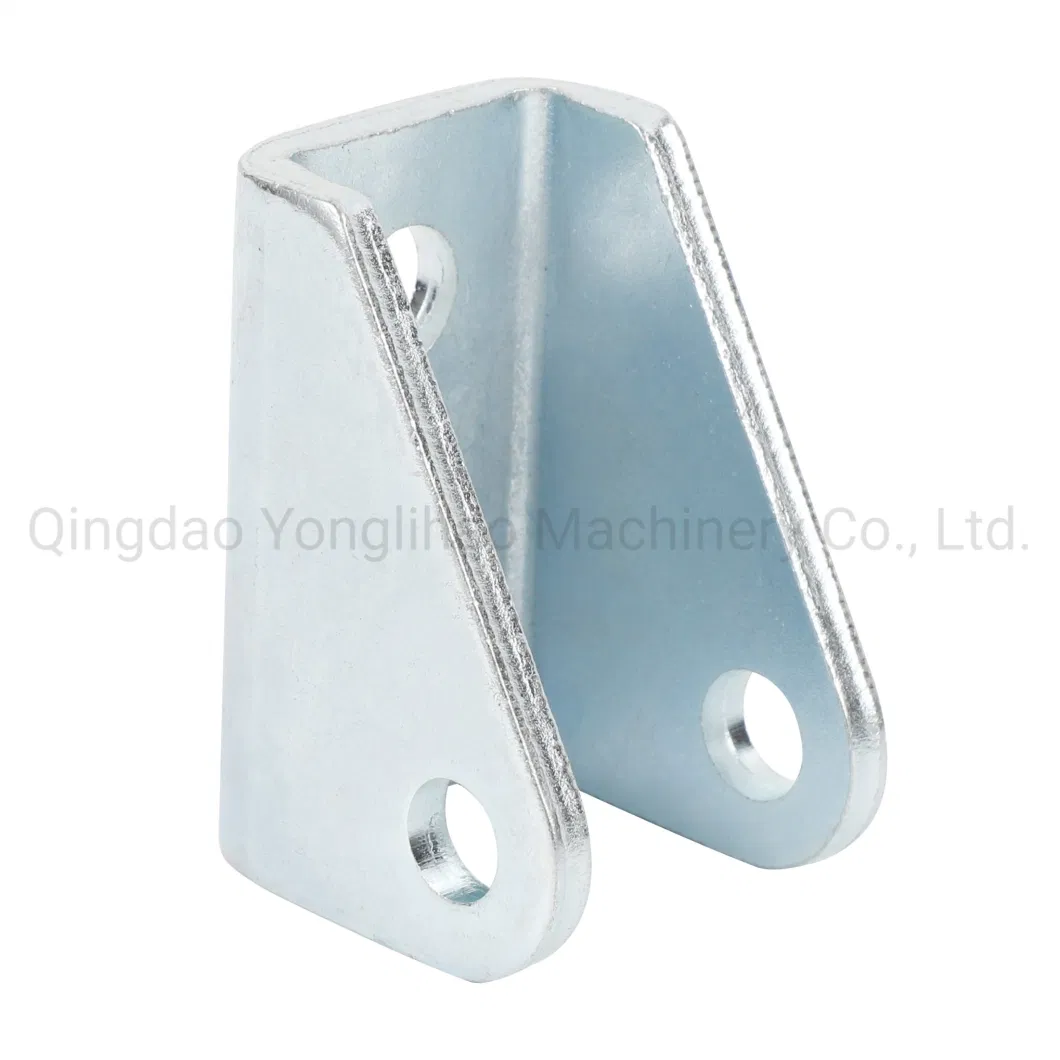
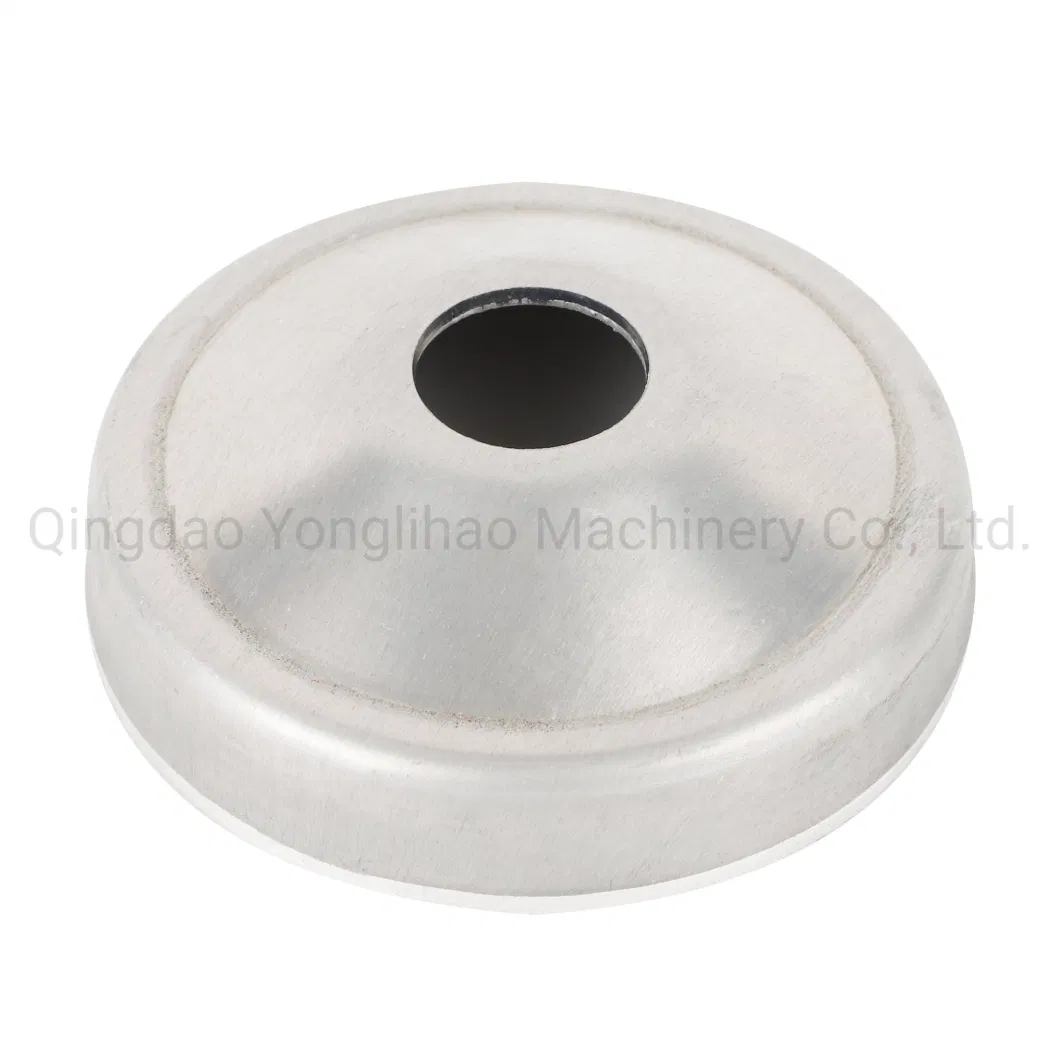
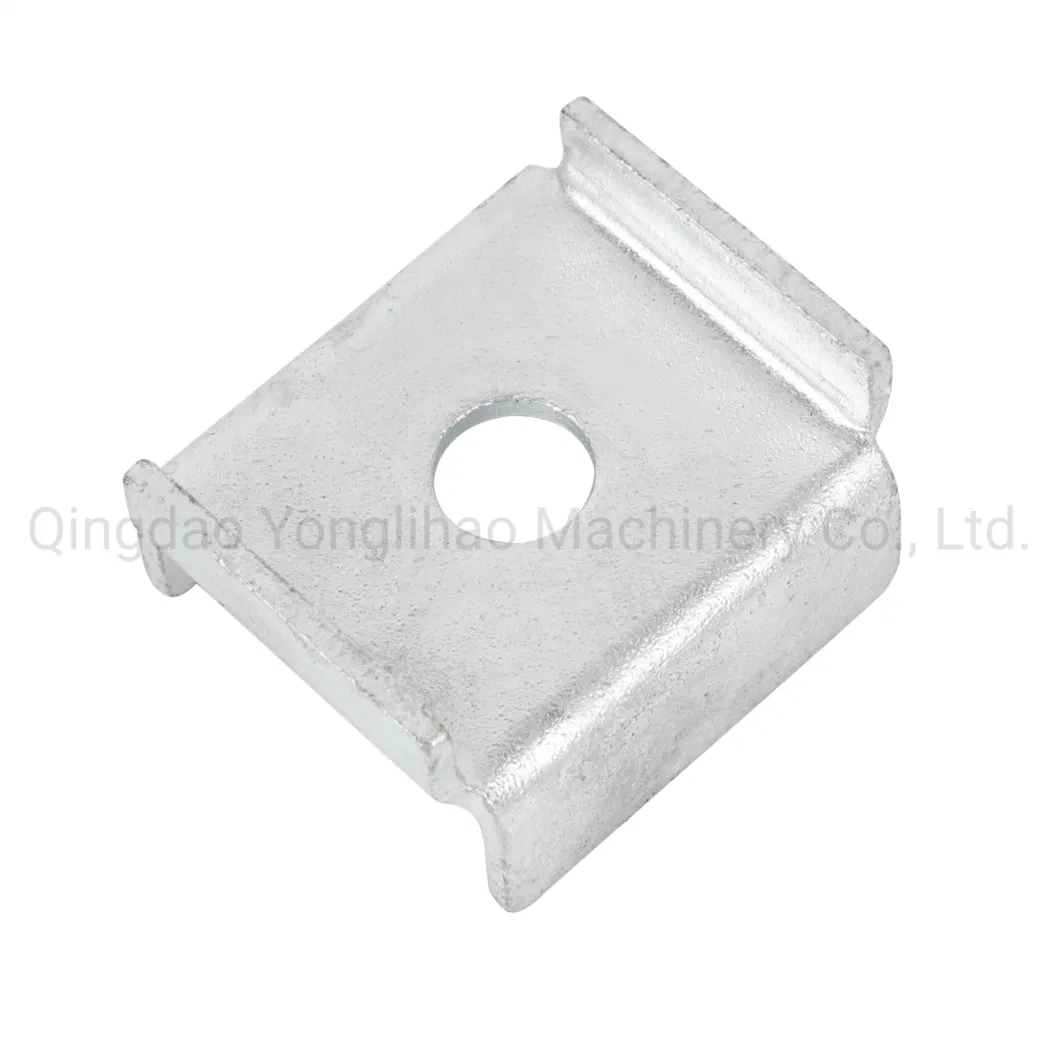
Welding Advantages:
1. argon tungsten arc welding:
1) Argon can effectively isolate air, is insoluble in metal and does not react with metal. During welding, the arc can also automatically remove the oxide film on the surface of the molten pool. Therefore, it can successfully weld non-ferrous metals, stainless steel and various alloys that are easy to oxidize, nitride and chemically active.
2) Tungsten electrode arc is stable, and dozens of it can still burn stably under a small welding current (less than 10a), which is especially suitable for the welding of thin plates and ultra-thin materials.
3) The heat source and filler wire can be controlled separately, so the heat input is easy to adjust, and welding at various positions can be carried out. It is also an ideal method to realize single-sided welding and double-sided forming.
4) Since the droplet of filler wire does not pass through the arc, no spatter will occur, and the weld formation is beautiful.
2. MIG welding:
1) Inert gases have little chemical interaction with any metal.
2) There is no coating layer on the surface of the welding wire, and the welding current can be increased. Therefore, the penetration of the base metal is large, the welding wire melting speed is fast, and the deposition rate is high. Compared with TIG (tungsten insert gas arc welding) welding, its production efficiency is high.
3) Droplet transfer mainly adopts jet transfer. Short circuit transition is only used in thin plate welding, while drop transition is rarely used in production. When welding aluminum, magnesium and their alloys, sub jet transition is usually used. Because the cathode atomization area is large, the molten pool protection effect is good, and the weld formation is good with few defects.
4) If short-circuit transition or pulse welding method is adopted, all position welding can be carried out, but its welding efficiency is lower than that of flat welding and horizontal welding.
5) Generally, DC reverse connection is adopted, so that the arc is stable, the droplet transfer is uniform, the splash is less, and the weld formation is good.
3. CO2 welding:
1) CO2 arc has strong penetration, which can increase the blunt edge of the groove and reduce the groove during thick plate welding; High welding current density and high welding wire melting rate; Generally, slag cleaning is not required after welding, so the productivity of CO2 welding is about 1 ~ 3 times higher than that of electrode arc welding.
2) Pure CO2 welding can not achieve jet transfer within the general process range. It is commonly used: short-circuit transfer and drop transfer. Jet transfer can be obtained only after mixed gas is added.
3) Short circuit transfer can be used for all position welding, and the welding quality of thin-walled components is high and the welding deformation is small.
4) It has strong rust resistance, low hydrogen content in weld, and little tendency to cold crack when welding low alloy high strength steel.
5) CO2 gas is cheap, and the cleaning of weldments before welding can be simplified. Its welding cost is only 40% ~ 50% of that of submerged arc welding and electrode arc welding.
4. submerged arc welding:
1) High welding productivity
2) Good weld quality
3) Low welding cost
4) Good working conditions
5) Wide welding range
5. resistance welding:
1) the two metals are heated internally under pressure to complete the welding. Whether it is the formation process of the welding joint or the formation process of the joint surface, its metallurgical problems are very simple.
2) Due to heat concentration and short heating time, the heat affected zone is small, and the deformation and stress are small. Generally, it is not necessary to consider the correction or heat treatment process after welding.
3) Simple operation, easy to realize mechanized and automated production, no noise and smoke, good working conditions.
4)With high productivity, it can be incorporated into the assembly line together with other manufacturing processes in mass production.
6. manual electrode arc welding:
1) The equipment used is relatively simple, relatively cheap and portable.
2) Gas protection is not required.
3) Flexible operation and strong adaptability.
4) It has a wide range of applications and is suitable for the welding of most industrial metals and alloys.
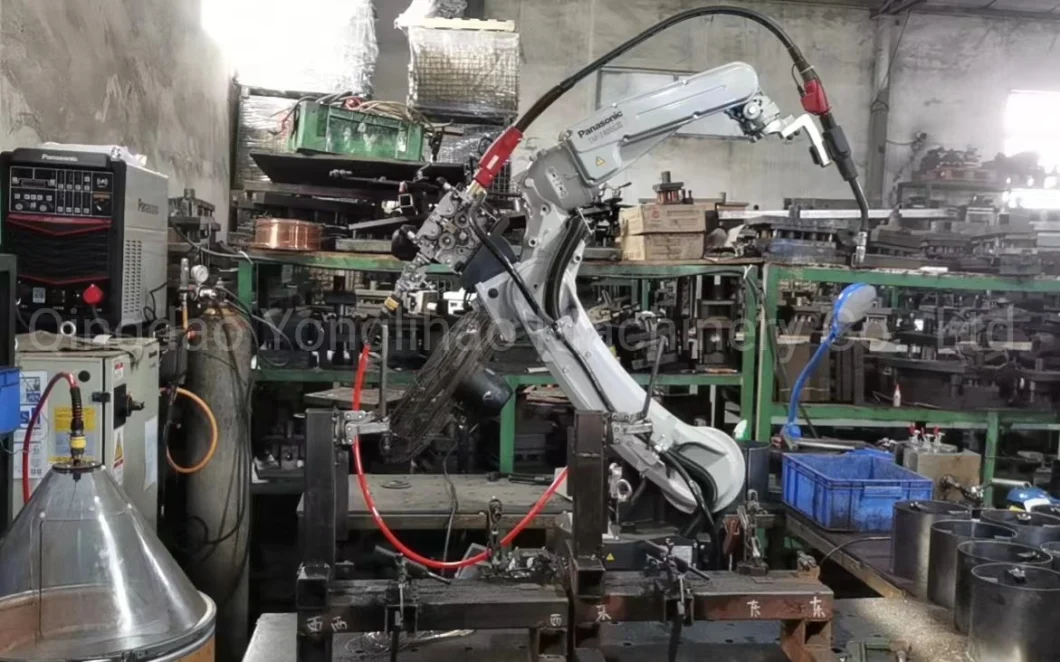
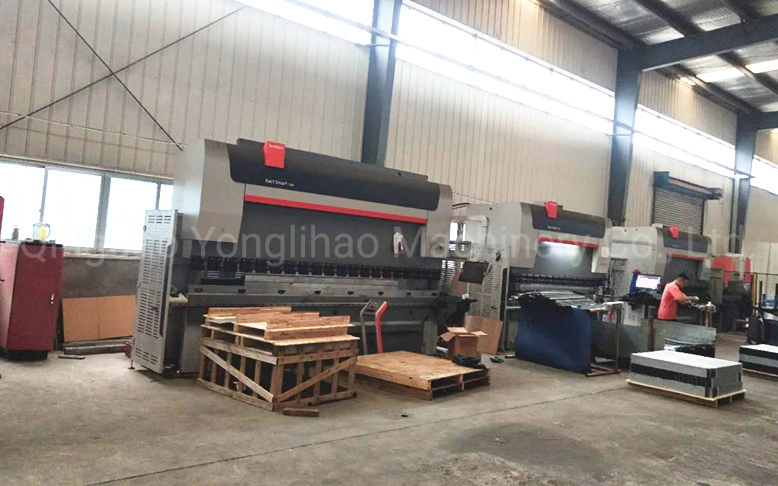
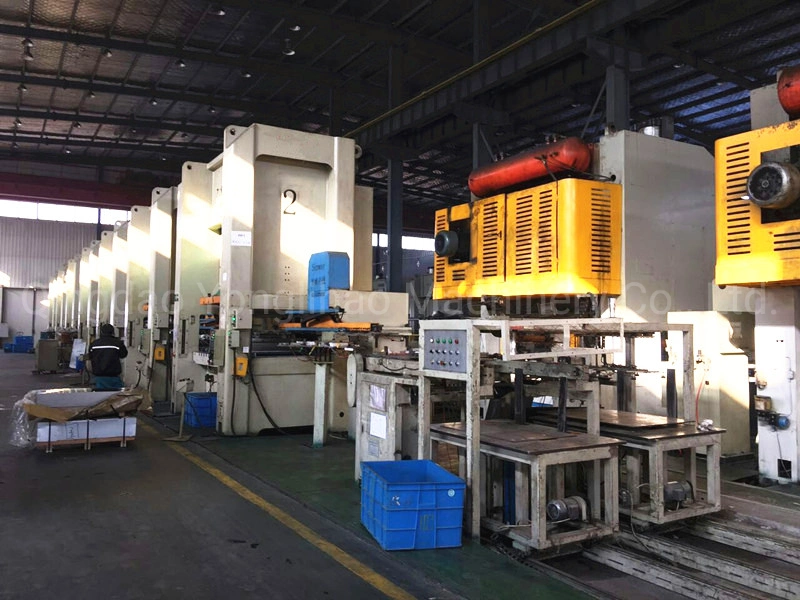
Production Process
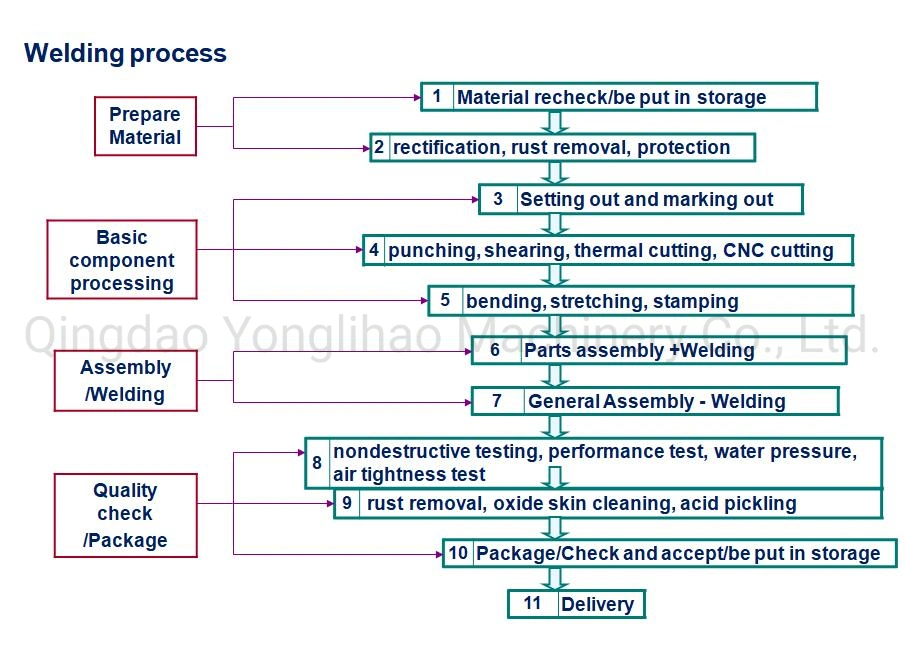
Quality Control
In Yonglihao, every staff emphasizes quality is first. Testing report and samples of all products will be kept by our quality control department.
>> Receiving inspection to raw material
All materials must be provided with suppliers' certificates, and have to pass the receiving inspection before starting production. Occasionally, material samples will be sent to independent lab for specific test to meet customers' demands. All materials have to be tagged and classified, so the original source could be traced at any time during production processes.
>> Producing inspection
Every phase of production processes will be monitored by producing inspection. The first product shall accept test in every phase of production process. Only it completes the test and confirmed by quality control manager, mass production could be operated. Every producing operator will implement constant tests during production processes, including size-measuring, observing the appearance.
>>Final inspection
Products of Yonglihao only can get out of the warehouses after all files signed and sealed.
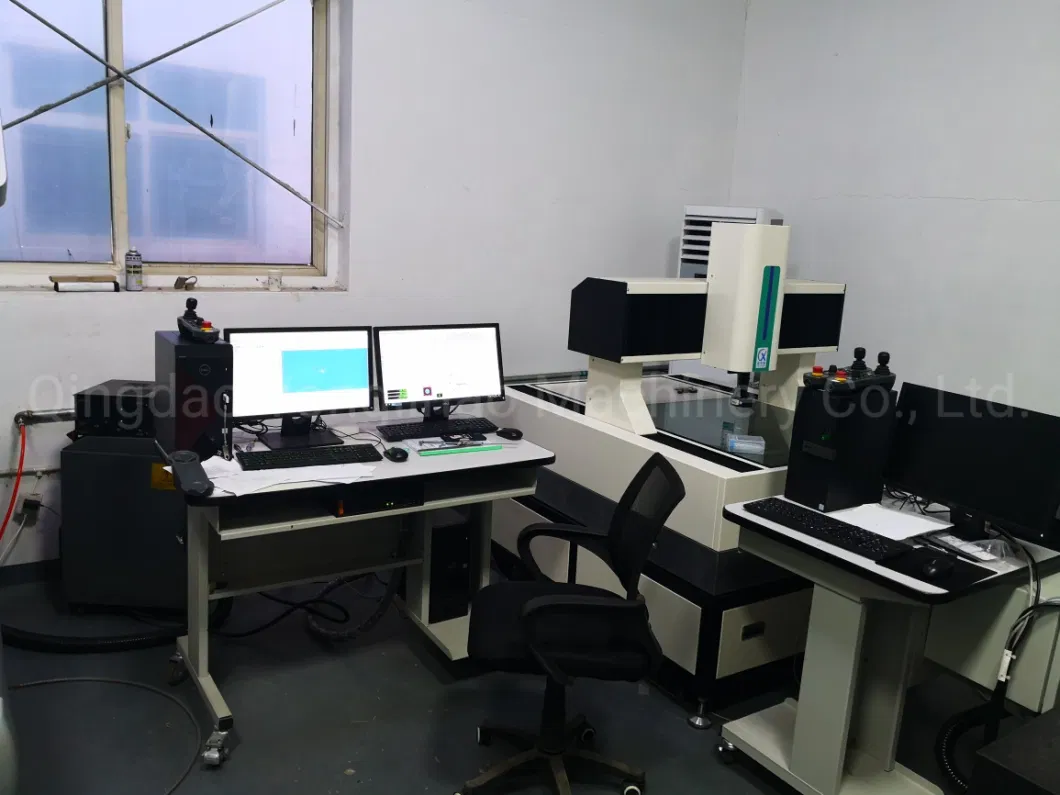
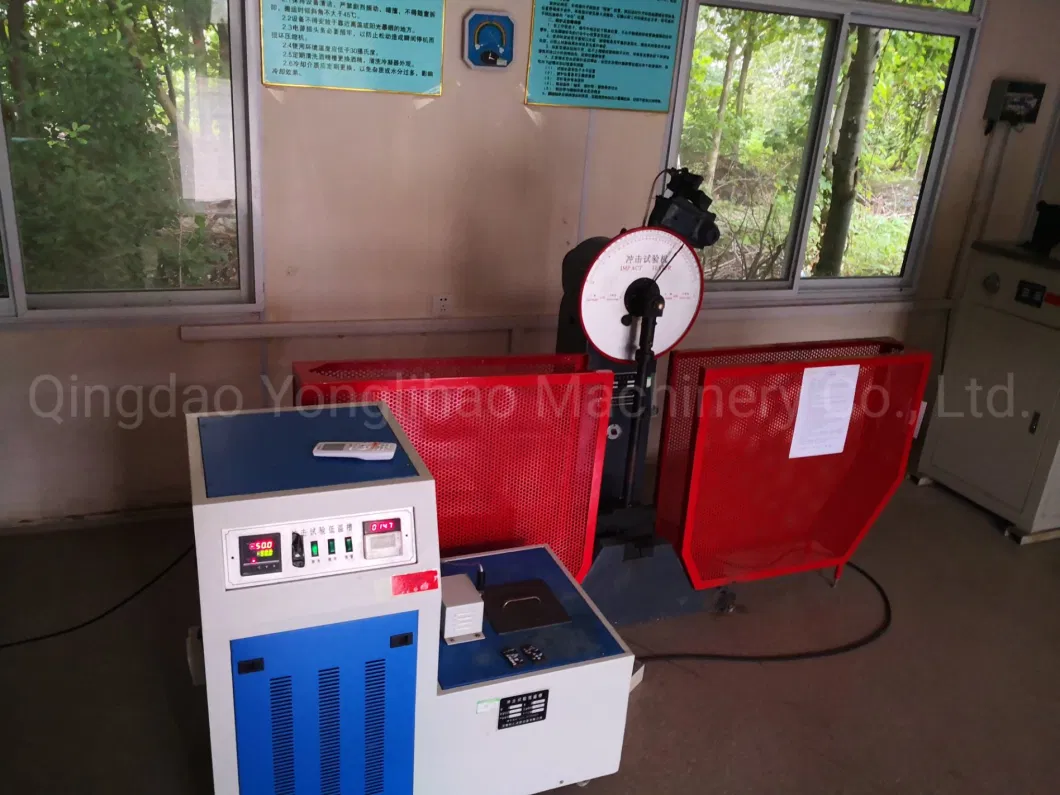
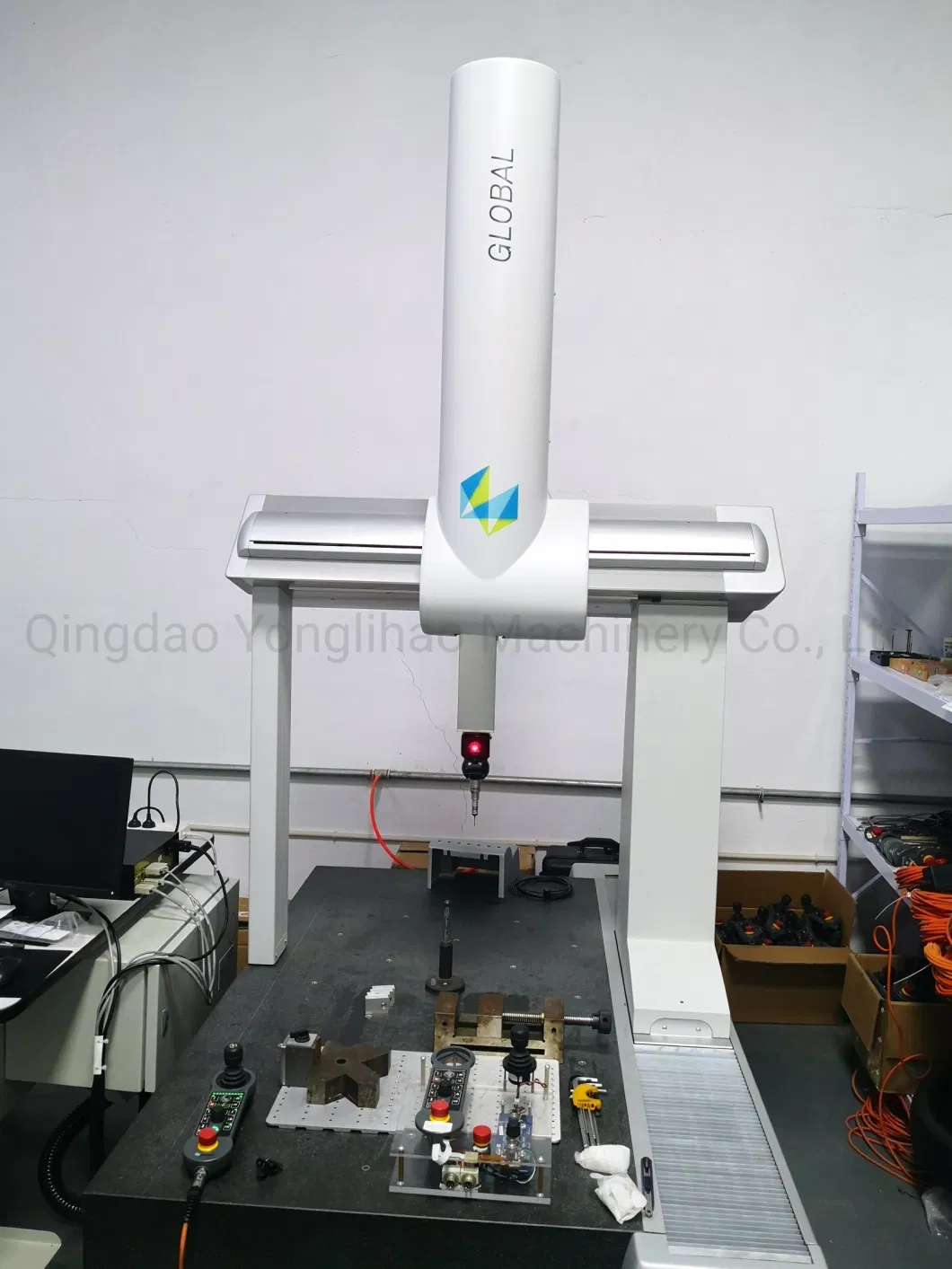
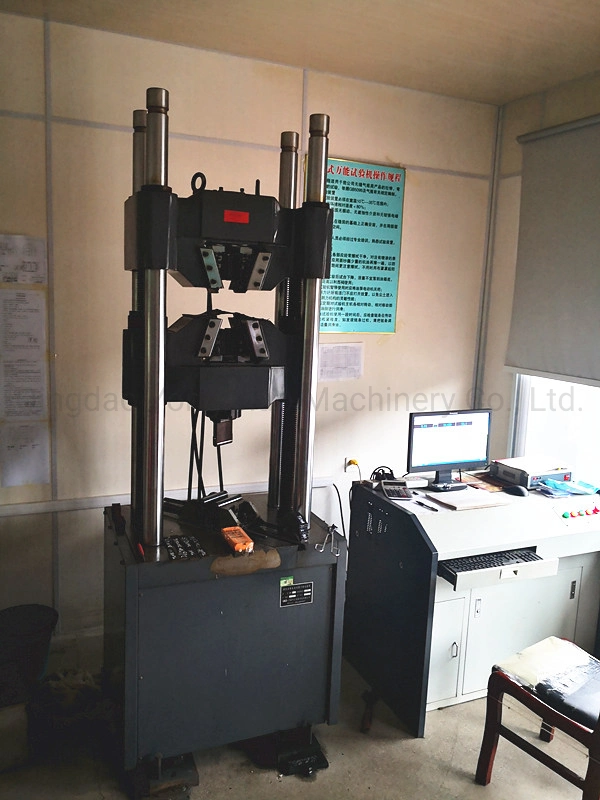
Warehouse and Shipment
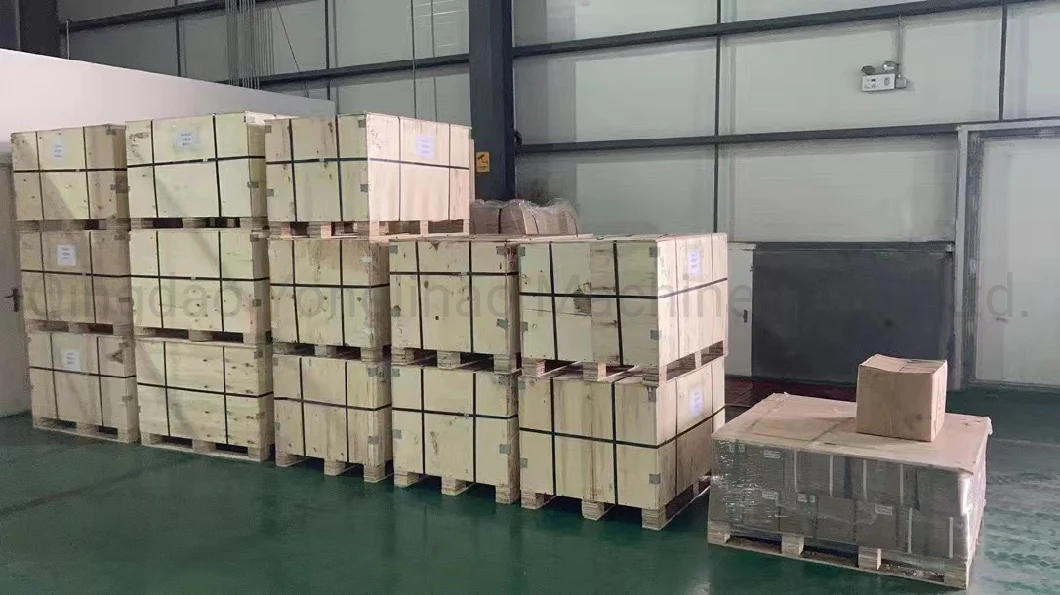
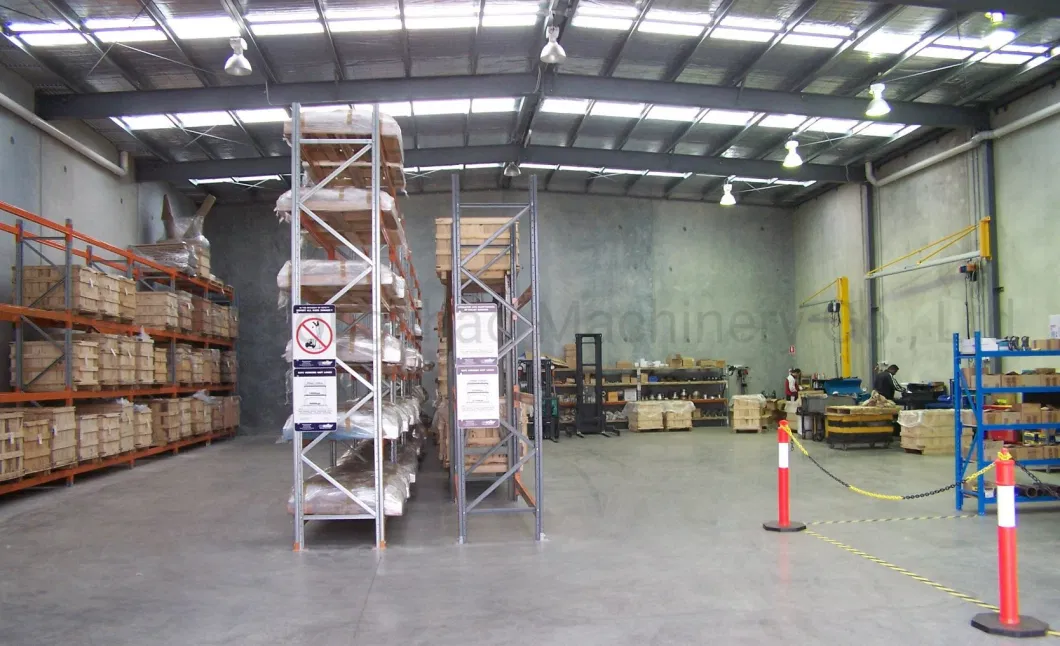

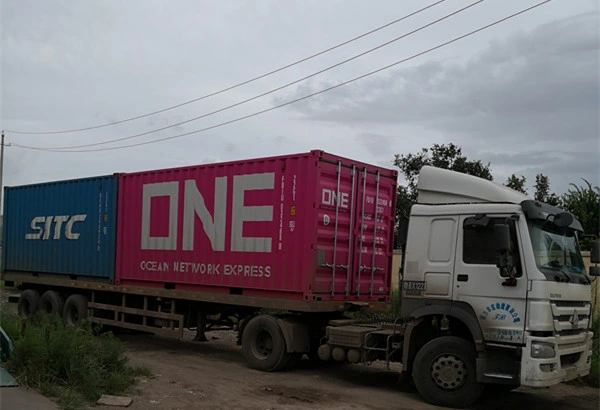
RFQ:
Q1:Where can I get product & price information?
A1:Send us inquiry e-mail or add us whatsapp, we will contact you as we receive your mail.
Q2:How long can i get the sample?
A2:Depends on your specific items, within 3-7 days is required generally.
Q3:What kinds of information you need for quote?
A3:Kindly please provide the product drawing in PDF, and will be better you can provide 3D drawing in STEP or IGS format.
Q4: What shall we do if we do not have drawings?
A4:Please send your sample to our factory, then we can copy or provide you better solutions. Please send us pictures or drafts with dimensions (Length, Hight, Width), CAD or 3D file will be made for you if placed order.
Q5: How can we know the chemical component of your products is according to our request?
A5: When we offer samples or batch parts, we will also send you our material list from our material factory, it shows more detailed.
Q6: How to guarantee your final size can meet our drawing request?
A6: we will make moulds according to your 3D drawing. And we also do sampling when batch production start, to make sure the final dimension can meet your request.
Q7: How to make sure the color after painting or powder coating can be correct?
A7: We have color card with different color number, such as RAL9016, we will contrast the sample surface and color card, to make sure the final surface effect is correct.
Q8: Generally, how do you packing the goods?
A8: normally, for inner package: the goods is nude, for outer package: carton + plywood.
Q9: If we find the defect products exist in the batch parts, how to do?
A9: Yes,your caution is very good, in fact, when batch production, we need do sampling. Before shipment, we also do testing to make sure the quality is ok. If you found several defect product exists, pls take photos and send your quality feedback, we will check and send you qualified products. But pls be assured that our products is qualified, unless caused by the worker's mistake to place.