- Overview
- Product Description
Basic Info.
Model NO.
SW39
Machining Method
Stainless/Aluminium/Copper/Brass/Carbon Steel
Material
Stainless/Aluminium/Copper/Brass/Carbon Steel
Name
Custom Sheet Metal Fabrication OEM Parts
Function
Sheet Metal Fabrication Service
Process
Sheet Metal Fabrication Stamping Bending
Color
OEM
Type
Laser Cutting Welding Stamping Bending
Certificate
SGS, ISO 9001:2015 & 14001:2015
Drawing Format
3D/CAD/Dwg//Step/Pdf
After Warranty Servicecity
Video Technical Support, Online Support
Customization
Yes!!
Feature
Top Quality and Used in High End Market
Shipping
Shanghai , Ningbo
Samples
7-15 Days
Transport Package
Pallet Box
Specification
OEM
Trademark
Sheetwell
Origin
Shanghai, China
HS Code
76109000
Production Capacity
900000
Packaging & Delivery
Package Size
1.00cm * 1.00cm * 1.00cm
Package Gross Weight
1.000kg
Product Description
What are the common processing technologies for automobile sheet metal parts?
1) Curling
Automotive sheet metal parts usually contain sharp edges with "hair" after initial production. Crimping is a forming process that involves deburring a metal plate to produce a smooth edge
2) Bend
Another common forming process of automobile sheet metal parts is bending. Companies usually use brake press or similar machine press to bend automobile sheet metal parts.
3) Ironing
It is also possible to charge metal plates to achieve uniform thickness. For example, most hat mirrors are made of iron. In the original state, the aluminum plate is too thick for the beverage, so it needs to be ironed to obtain thinner and more uniform ingredients
4) Laser cutting
In recent years, laser cutting has become a more and more common forming process for automotive sheet metal parts. Through laser cutting, the metal plate is exposed to a high-energy laser and burns holes in the metal.
5) Hydroforming
A little-known forming process of automobile metal parts is hydraulic forming. Like deep drawing, hydraulic forming involves drawing wool on the mold. So what is the difference between hydroforming and deep drawing? The main difference between these two processes is that deep drawing needs to reduce drawing many times, while hydraulic forming can be completed in only one step.
6) Punching
Stamping is a forming process of automobile sheet metal parts, which involves punching holes in automobile sheet metal parts with punches and dies. Automobile sheet metal parts are placed between punches and die, and then punches are pressed down and pass through metal plates to form a hole
1) Curling
Automotive sheet metal parts usually contain sharp edges with "hair" after initial production. Crimping is a forming process that involves deburring a metal plate to produce a smooth edge
2) Bend
Another common forming process of automobile sheet metal parts is bending. Companies usually use brake press or similar machine press to bend automobile sheet metal parts.
3) Ironing
It is also possible to charge metal plates to achieve uniform thickness. For example, most hat mirrors are made of iron. In the original state, the aluminum plate is too thick for the beverage, so it needs to be ironed to obtain thinner and more uniform ingredients
4) Laser cutting
In recent years, laser cutting has become a more and more common forming process for automotive sheet metal parts. Through laser cutting, the metal plate is exposed to a high-energy laser and burns holes in the metal.
5) Hydroforming
A little-known forming process of automobile metal parts is hydraulic forming. Like deep drawing, hydraulic forming involves drawing wool on the mold. So what is the difference between hydroforming and deep drawing? The main difference between these two processes is that deep drawing needs to reduce drawing many times, while hydraulic forming can be completed in only one step.
6) Punching
Stamping is a forming process of automobile sheet metal parts, which involves punching holes in automobile sheet metal parts with punches and dies. Automobile sheet metal parts are placed between punches and die, and then punches are pressed down and pass through metal plates to form a hole
1. Raw Material | Copper, phosphor copper, Brass, Stainless steel, Aluminum, steel, spring steel, Nickel-Silver... and all different kinds of metal; |
2. Surface treatment | Gold / Silver /Tin / Nickel / Zinc / Chromium / Copper-plating / Laser etching/Screen printing/Phosphating (can pass salt spray testing with 160 hours)/Black coating / Painting/ Power coating /Electrophoresis / Passivating /Deburring / Polishing / Brush according to ROHS standard; |
3. Quotation | Please provide the Formal drawings (normally, with DWG/STP/PDF file ), and make notes with material/QTY/surface treatment and any other requirements, we will provide you the quotation sheet within 48-72 hours; |
4. Prototype & Mould | We make the prototypes or molds according to the drawings confirmed by both of us and the customers! The lead time depends on the structure and qty of parts, Normally, the lead time for prototypes is 3-15 days; the lead time for mold is 10-25 days; |
5. Production | We will provide samples according to the drawings to customers for approval. Then arrange the production and confirm the delivery date according to the Purchase Order; Normally, the lead time for production is 5-30 days, the structure of parts is different, and the lead time will be different. |
6. Package | Plastic bags; Preserving Box; Reel/tape package; Plastic tray; Wood box; Export carton and any other customized package according to the customers' requests. |
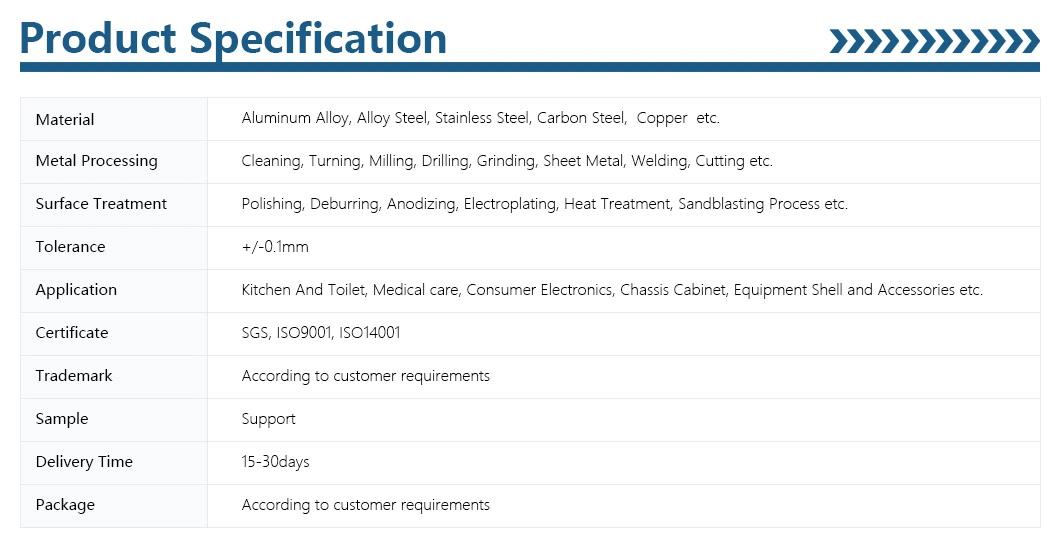

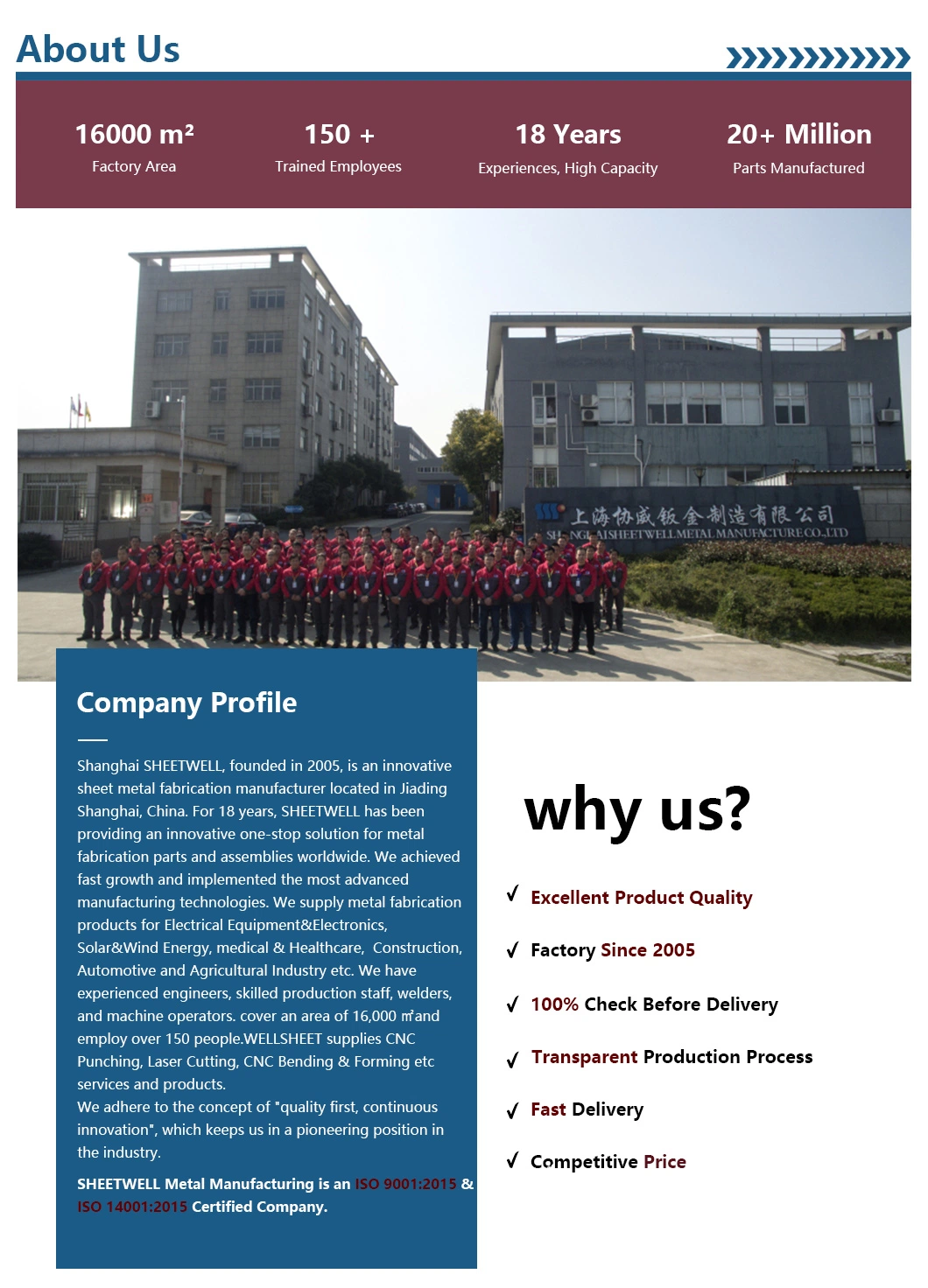
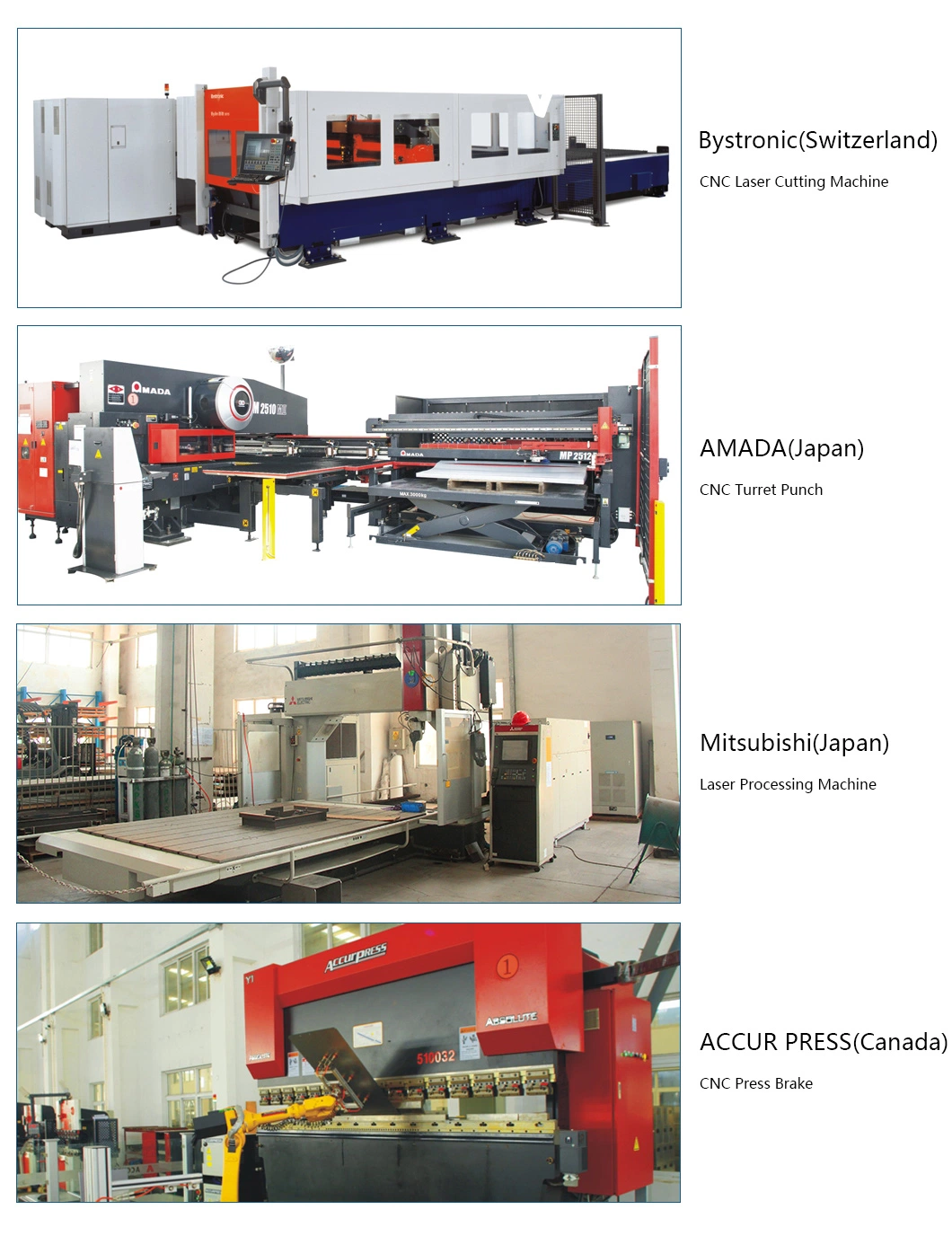
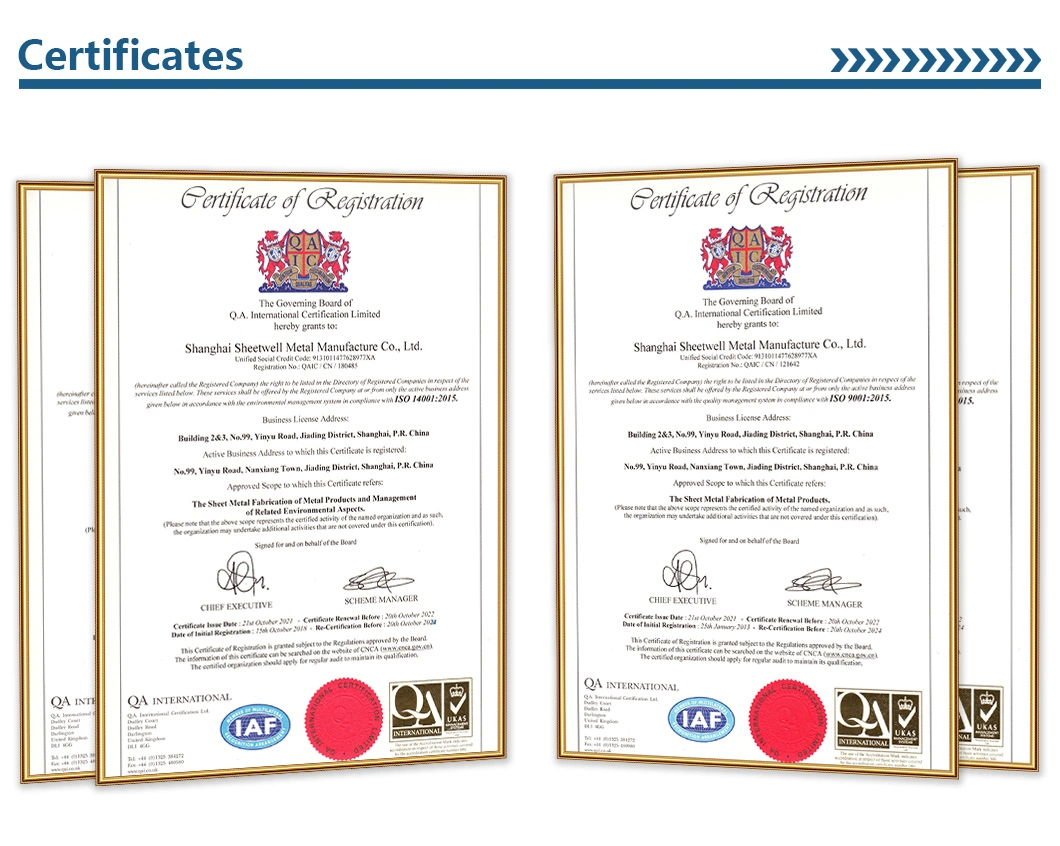
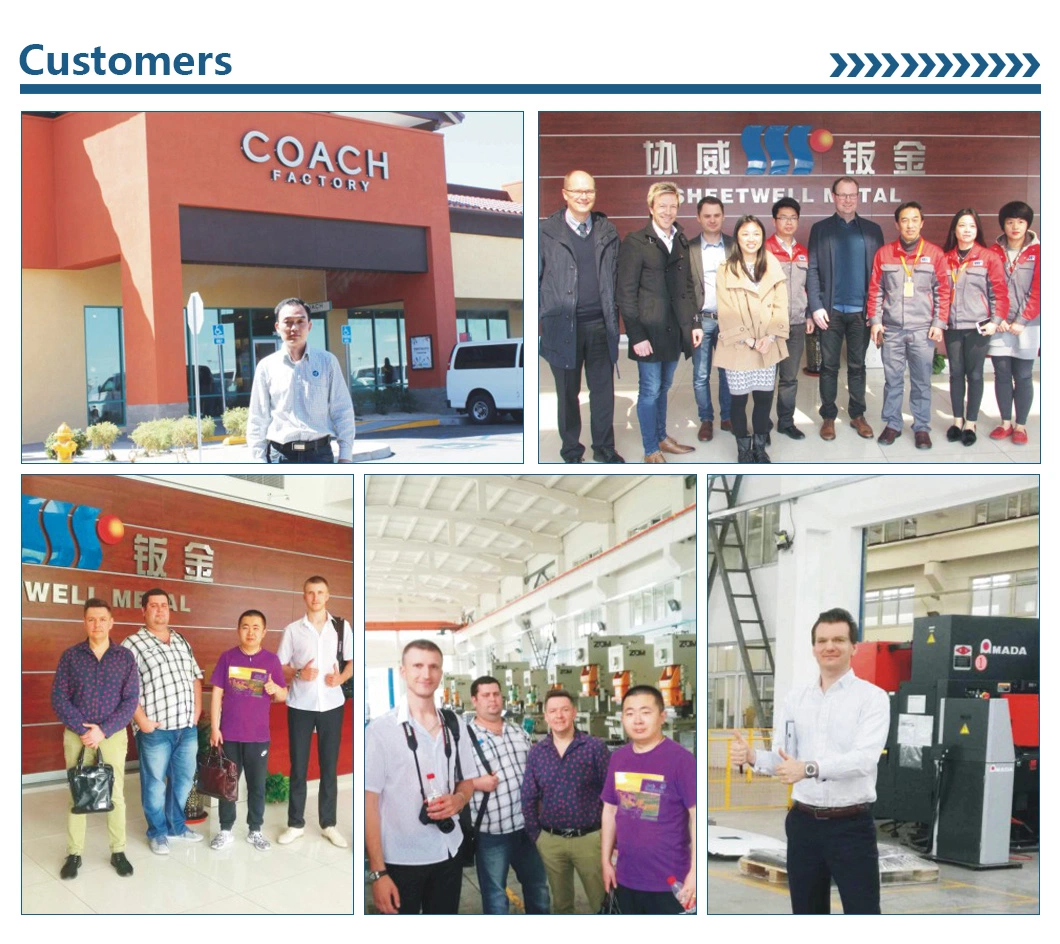
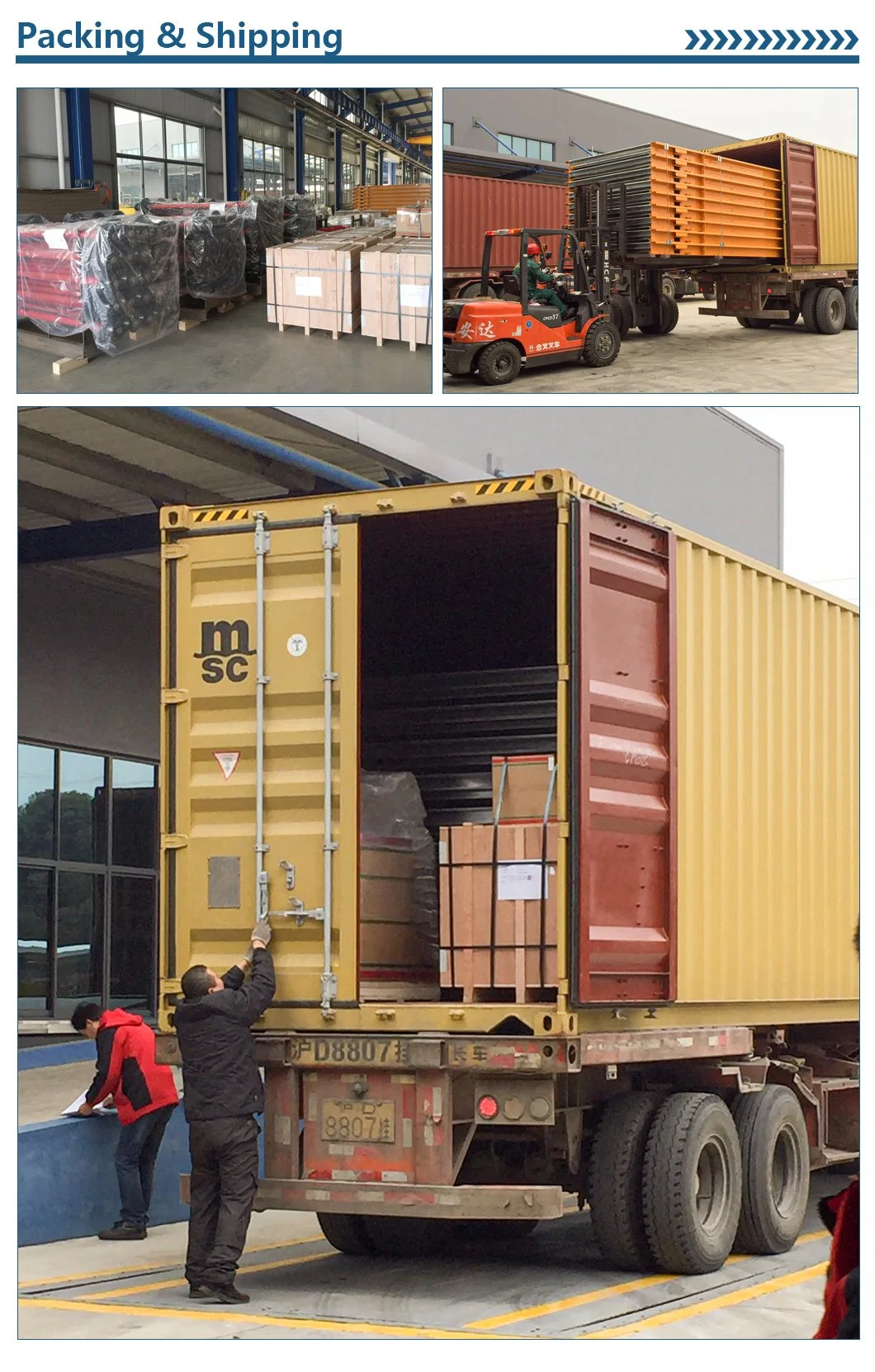
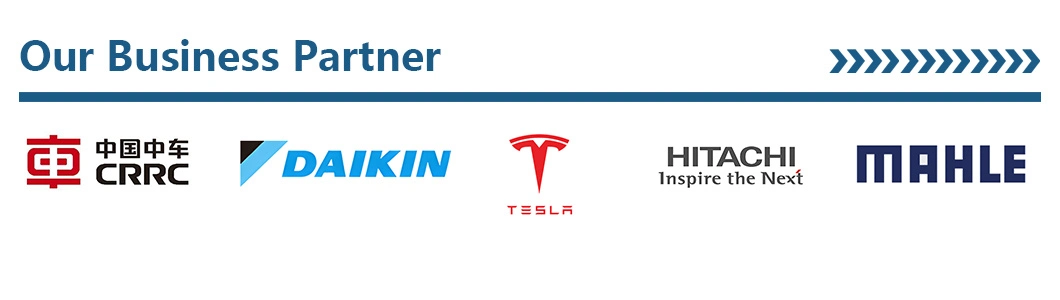